Az alábbi vendég posztunk írója a Leannovation folyamatfejlesztési tanácsadója, Pető Sándor.
A lean szemlélet minden nap arra törekszik, hogy a dolgozók bevonásával, folyamatos fejlesztésekkel csökkentse a termelés során esetlegesen felmerülő veszteségeket. Ezen tevékenységeknek a „vevője” a soron vagy a műhelyben dolgozó kolléga, akinek, ha a munkáját egyszerűbbé, könnyebbé tesszük, akkor a termelés mind a munkabiztonság, minőség, hatékonyság, mind pedig a termelékenység szempontjából eredményesebb lesz.
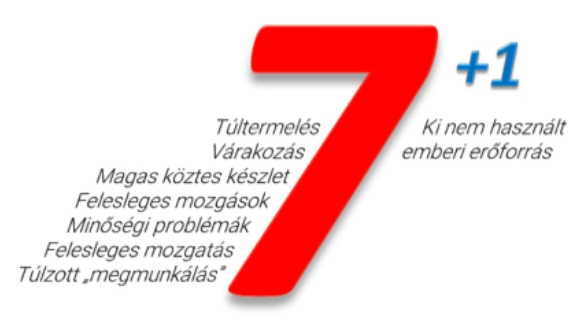
A lean által vizsgált 8 veszteség közül az egyik a felesleges mozdulatok. Tapasztalataink szerint számszerűsége alapján ez a veszteség fajta vezető helyen szerepel a többivel szemben. Ugyanakkor azt is el tudjuk mondani, hogy a mozdulatelemzési tevékenységeket (motion kaizen, motion economy) leginkább azok a cégek végzik, akiknek már magas lean fejlettségi szintjük van, emiatt a lean transzformáció során nem ezzel a feladattal kezdünk.
Ezzel a témával nem ma kezdtek el foglalkozni először, a 20. század elején már Gilbreth tanulmányozta a mozdulatokat. Építőipari vállalkozóként kőműveseinek tevékenységét vizsgálta meg, megfigyeléseit filmre vette és időmérésekkel kielemezte. A szerzett tapasztalatok alapján a munkavégzési folyamatot 17 alapmozdulatra bontotta, melyeket 3 fő csoportra osztott: megragadás, mozgatás, megtartás. Nemcsak fizikai, hanem az indirekt tevékenységet folytató kollégáit is megfigyelte. Tanácsadóként a menedzsereket arra tanította, hogy mindig kérdőjelezzék meg a munka elvégzésének módját és felhívta a figyelmet a folyamatos fejlesztés jelentőségére – mintha csak egy lean tanácsadót hallanék, pedig akkor még nem volt sehol sem a lean, de még a Toyota Gyártási Rendszere sem
1948-tól a mozdulatok standard idejének meghatározásához használják az MTM (methods-time measurement) módszert is. A vizsgálat során videóra veszik a mozdulatokat, majd részletes időelemzést végeznek és meghatározzák az elvárható standard időt az adott tevékenység elvégzéséhez.
Az ergonómia központjában, mint ahogy a lean menedzsmentben is, az ember áll, hiszen, ha a dolgozónak is jó, akkor az egész szervezetnek (egészséges, motivált munkavállaló), az egész cégnek is jó lesz (termelékenység, profit).
Ha meg akarjuk érteni a nehézségeket, a problémákat, akkor el kell mennünk a genba-ra (ahol a dolgok történnek – ez lehet a termelés vagy akár az iroda is), és meg kell figyelni és érteni: az embert, a gépet, a környezetet és a folyamatot is. Kockázatelemzéssel felmérhetők a legkevésbé ergonomikus munkahelyek, ahol a dolgozó felesleges és nehéz mozdulatokat csinál.
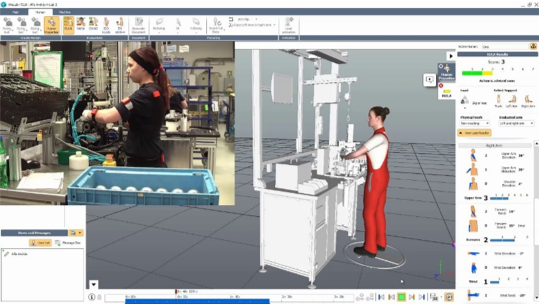
Erre napjainkban már létezik egy fejlett megoldás, mely a mozgást szenzorokkal rögzítve és szoftverrel elemezve részletes és objektív elemzést ad, ez pedig a ViveLab. A szoftver által generált riport kiemeli azokat a mozdulatokat, melyeket ki kell küszöböli, erre pedig a mérnökökből és ergonómusokból álló szakértői csapat ad megoldási javaslatokat.
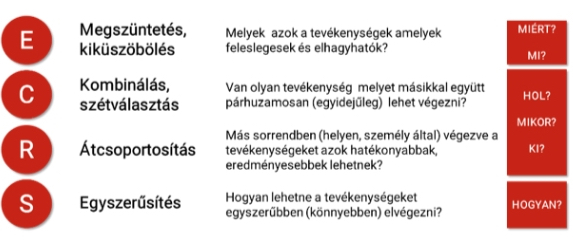
Ezeket a fejlesztéseket érdemes kombinálni a folyamatokra és munkaállomásra vonatkozó ECRS (Eliminate, Combine, Rearrange, Simplify) megközelítéssel.
Ehhez első lépésben azon elemeket határozzuk meg, amik megszüntethetők, kiküszöbölhetők. Második lépésben azon tevékenységeket határozzuk meg melyeket egyszerre, párhuzamosan is lehet végezni. Harmadik lépésben a sorrendet vesszük górcső alá, hogy megtaláljuk az ideális, leghatékonyabb sorrendet. A negyedik lépés pedig az egyszerűsítésről szól.
Az ergonómiai és az ECRS fejlesztések nemcsak a veszteségeket csökkentik (növelik az értékteremtés arányát) és teremtenek jobb, az egészség szempontjából is kedvezőbb munkavégzést, hanem jelentős ciklusidő csökkentést eredményeznek a gyártási folyamatokban. Ezért ezen fejlesztéséket célszerű összekapcsolni egy ciklusidőt és kiegyensúlyozást vizsgáló elemzéssel.
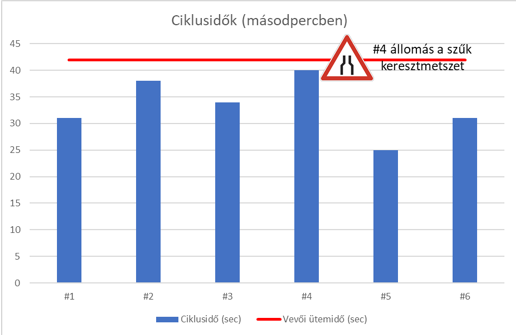
A feladatot a vevői ütemidő meghatározásával kezdjük. Ez az az idő (piros vonal), amely meghatározza, hogy a vevőnk mennyi időnként akar tőlünk 1 db terméket megkapni. Ez azért fontos, mert a folyamatunk ciklusideje nem lehet ennél nagyobb, mert ha így lenne, akkor nem tudnánk kielégíteni a vevői igényeket. Az elemzés során felmérjük az egyes állomások gépi és operátori ciklusidejét. Ez alapján készül el a mellékelt ábrán szereplő oszlopdiagram. Ha az operátori tevékenység (#4-es állomás) ciklusideje a legnagyobb, akkor az ergonómiai fejlesztések során nyert ciklusidő csökkentéssel javíthatunk ezen. Az ebből nyert másodpercek mind-mind növelik a sorunkon gyártható darabszámot és termelékenységet, viszont ez a kapacitásbeli többlet nem szabad, hogy túltermelést eredményezzen! Az időbeli nyereséggel a túlórák és műszakok számát csökkenthetjük, valamint a szabad kapacitást újabb termékek gyártásra fordíthatjuk.
Ezeknek az eszközöknek és fejlesztési folyamatoknak, mint minden máslean eszköznek is az a célja, hogy felszínre hozza a problémákat. A dolgozók ésa céges érdekek egyeztetésével és a lean segítségével megalkothatjuk ahatékonyság szimfóniáját!
Regisztráljon a Lean on the Beach szakmai napra!
Az ergonómia 21. századi elemzésével és fejlesztésével is foglalkozik a Lean on the beach konferencia, 2019. július 3-án, a Budapest Holiday Beach hotelben, ahol nyári hangulattal, szabadságok előtti szakmai feltöltődéssel és Lean Coffee hangulattal várjuk a résztvevőket.
A további programot és a jelentkezést ezen a linken találják: http://leannovation.hu/esemeny/lean-on-the-beach_2019/